More info
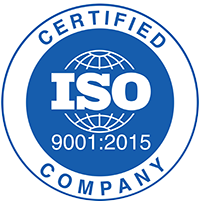
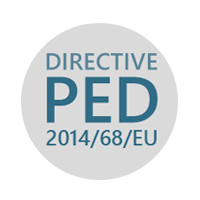
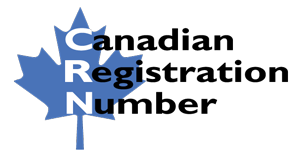
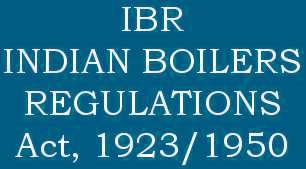
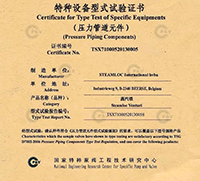
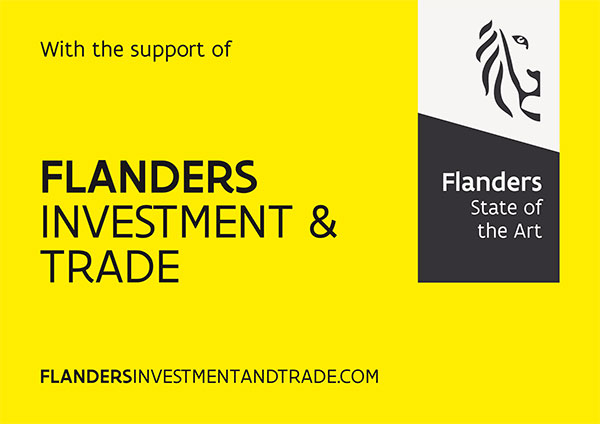
At start-up, gradually building pressure will release air and non-condensables first since there is no condensate yet. Once the heat-up load flows in, Steamloc® has sufficient overcapacity to deal with it. As condensate forms from the normal process of exchanged heat, it flows into our Steamloc® by gravity, together with the present steam. At first glance, heavy and slow condensate is expected to be found in the bottom while the light and fast steam must be in the top section of the venturi set. Considered as such, a lot of steam would be passing. Happily, in a well-designed restriction, the actual flow pattern is completely different from such a split laminar flow.
In a well-shaped venturi/nozzle/orifice, the condensate and steam will propel through as a turbulent dispersed and mixed 2-phase flow. Live steam is impeded to pass easily because of different physical conditions between the liquid and the gas, such as density and velocity, laminar and turbulent flows, compressing and expanding effects. But also the coalescence flowing of gas and liquid parts that impact particle-wall and inter-particle collision, … while Bernoulli and energy levels play their role too. These effects are happening simultaneously from the entrance up to the outlet zone.
Another effect for not passing steam is the flash steam generation. While approaching the condensate zone, the pressure drop sets in and from nature, part of the condensate will transform into flash steam due to the difference in energy level in the up- and downstream of the venturi. This flash also has impact to limit the steam slip although to a lesser extent than often said.
Rather than generalizing, we can imagine your application might have different characteristics than others. How do you start-up? Do loads change? Is there fouling? What happens at a pressure drop? What about a wide pressure range? Is there impact of superheated steam? … So many details can make your applications unique.
We will evaluate and document each steam trap station, grouped or stand-alone, by means of a unique Steamloc® datasheet. No worries, we use the same data as you have already available for your traps.
And with your permission, we use this same data to cross-check a few things that might be of interest for your installation. As a co-engineering partner, we can employ our years of expertise to ensure a long lifetime for your whole installations. Long may you run!
Steamloc® is based on a modified multi-configured venturi jet and designed to enhance the condensate flow and at the same time inhibit passage of live steam. It uses the different characteristics from both incoming phases to ensure sufficient drain and minimize energy consumption at all times.
There are no moving parts to fail and when properly sized and installed, it performs at least equal, and likely better than mechanical traps in normal operation. The fact Steamloc® cannot fail and spoil will make the switch widely worth it. Typical ROI calculations that use your numbers are expressed in terms of months.
The installed capacity depends on differential pressures and loads. Each application has its unique Steamloc® which perfectly handles its running loads. Steamloc® is available for loads from <5 kg/h upwards to massive loads of 150.000 kg/h and more at differential pressures even higher than 150 bar, but also for the tiny pressure differences balancing with vacuum where mechanical traps do not even work at all.
Steamloc® can be applied on all kinds of applications. While mechanical traps are chosen from a catalogue and often oversized, we will customize a matching Steamloc® for each of your process traps. The numerous utility traps will be group-selected by type, pressure and duty.
For all your traps, Steamloc® is the final and once-only action, to be done just one single last time. For each application. From then, you avoid any 'cost of ownership' and save money on the long term.